How Preventive Maintenance Scheduling Can Cut Costs and Minimise Downtime
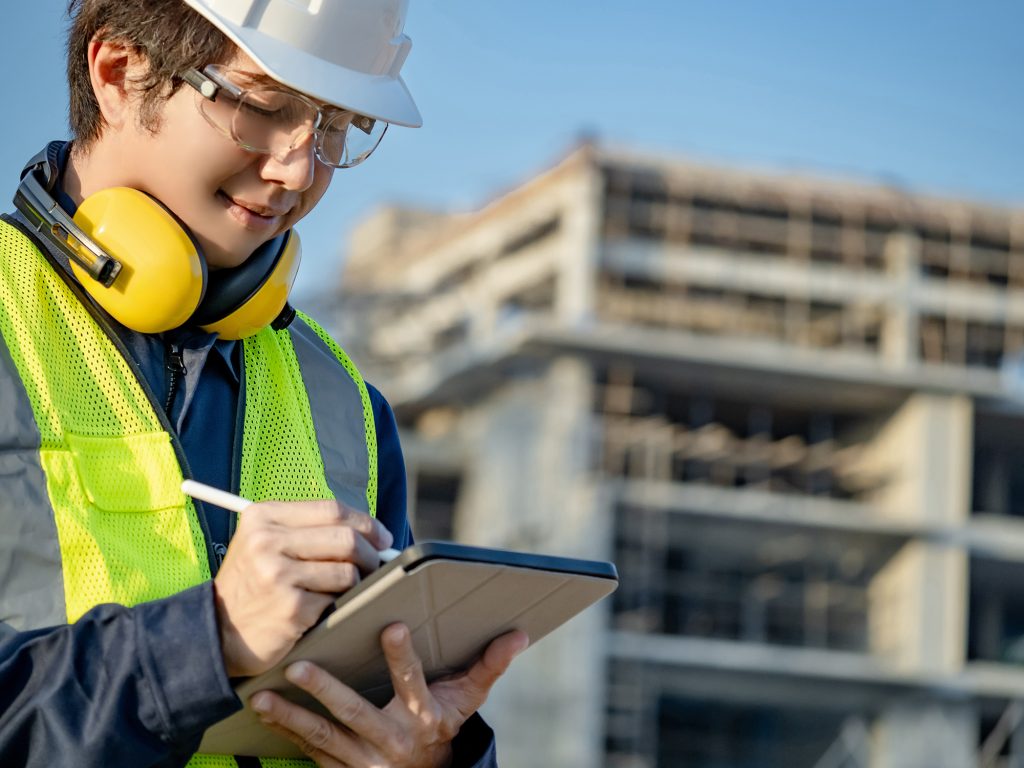
Preventive maintenance (PM) is a proactive approach that involves regularly scheduled inspections, servicing, and repairs to keep equipment in good working order. Rather than waiting for machinery or systems to fail, preventive maintenance aims to detect and address potential issues before they cause costly breakdowns. Implementing a preventive maintenance schedule can significantly reduce expenses, improve efficiency, and minimise downtime. In this article, we’ll explore the benefits of preventive maintenance scheduling and how it can help businesses save on costs while boosting productivity.
The Basics of Preventive Maintenance Scheduling
Preventive maintenance scheduling is the process of planning routine maintenance tasks for equipment or systems based on time intervals or usage. By establishing a consistent maintenance schedule, businesses can ensure that equipment is inspected, cleaned, lubricated, or repaired regularly to prevent unexpected failures.
For example, a manufacturing company might schedule regular maintenance for its machinery every 500 hours of operation, while a facilities management team could arrange HVAC inspections every three months. The key is to establish a schedule that aligns with the specific needs of each piece of equipment or system.
How Preventive Maintenance Helps Reduce Costs
1. Avoiding Expensive Emergency Repairs
Emergency repairs are not only inconvenient but can also be far more expensive than routine maintenance. When equipment fails unexpectedly, it often requires urgent attention, which can lead to higher costs for labour, parts, and even overtime work. Preventive maintenance helps identify potential problems early on, allowing for timely, cost-effective repairs that prevent more severe and costly issues from arising.
2. Extending Equipment Lifespan
Regular maintenance helps extend the lifespan of equipment by keeping it in optimal condition. By addressing minor issues before they escalate into major problems, businesses can avoid premature wear and tear that leads to early equipment replacement. This reduces capital expenditure on new equipment and allows organisations to get the most out of their existing assets.
3. Minimising Production Downtime
Unplanned equipment breakdowns can bring production to a halt, causing costly downtime. Scheduling preventive maintenance during planned downtime or slower periods allows businesses to perform necessary repairs and servicing without disrupting operations. This approach ensures that equipment remains operational when it’s needed most, helping to maintain steady production levels and minimise revenue losses.
4. Reducing Energy Costs
Well-maintained equipment runs more efficiently, which can lead to energy savings. For example, HVAC systems that receive regular cleaning and servicing operate more effectively, consuming less energy to maintain desired temperatures. Similarly, machinery that is regularly lubricated and adjusted will use less power, resulting in lower energy bills for the business.
5. Improving Safety and Reducing Liability Risks
Equipment failures can pose significant safety risks, leading to accidents or injuries. Preventive maintenance helps ensure that machinery and systems operate safely, reducing the likelihood of incidents. This not only protects employees but also minimises the risk of liability claims and associated costs.
The Role of Preventive Maintenance Scheduling Software
While the benefits of preventive maintenance are clear, managing maintenance schedules manually can be challenging, especially for businesses with a large inventory of equipment. This is where preventive maintenance scheduling software comes in. These digital tools automate the planning and tracking of maintenance tasks, making it easier to keep on top of schedules and ensure that no tasks are missed.
Here’s how preventive maintenance software can support your maintenance efforts:
1. Automating Maintenance Reminders
Software solutions can automate maintenance reminders based on usage data or pre-set time intervals, ensuring that tasks are never overlooked. This helps to keep all equipment in optimal condition and reduces the chances of unexpected breakdowns.
2. Tracking Maintenance History
Preventive maintenance software records maintenance activities, providing a complete history for each piece of equipment. This information can be used to identify patterns, predict future maintenance needs, and make more informed decisions about repairs or replacements.
3. Improving Resource Allocation
With a clear overview of upcoming maintenance tasks, businesses can allocate resources more effectively. Maintenance teams can be scheduled based on priority, ensuring that critical tasks are addressed promptly while avoiding overloading technicians with last-minute requests.
4. Enhancing Compliance with Industry Regulations
Many industries have strict regulations regarding equipment maintenance. Preventive maintenance software helps businesses stay compliant by keeping detailed records of maintenance activities and ensuring that all tasks are completed on time. This can help avoid fines or penalties related to regulatory non-compliance.
Best Practices for Implementing a Preventive Maintenance Schedule
To maximise the benefits of preventive maintenance scheduling, businesses should consider the following best practices:
1. Assess Your Equipment and Prioritise Maintenance Needs
Begin by evaluating all equipment to determine which assets are most critical to your operations. Prioritise maintenance tasks based on factors such as equipment age, usage frequency, and failure history. Focusing on high-priority equipment ensures that resources are allocated effectively and that the most essential assets remain in good condition.
2. Establish a Realistic Maintenance Schedule
Create a maintenance schedule that aligns with the specific needs of your equipment. Consider factors like manufacturer recommendations, usage patterns, and operational demands. It’s important to strike a balance between performing maintenance too frequently (which can be unnecessarily costly) and too infrequently (which increases the risk of breakdowns).
3. Use Preventive Maintenance Software to Stay Organised
Take advantage of software tools to automate scheduling, track maintenance history, and generate reports. This will help you stay organised and keep maintenance tasks on track. The software can also help you adjust the schedule as needed based on changing operational conditions or equipment performance.
4. Train Your Maintenance Team
Ensure that maintenance personnel are well-trained in using preventive maintenance software and following established procedures. Proper training helps teams perform maintenance tasks correctly and efficiently, which is crucial for maximising equipment performance and longevity.
5. Monitor and Adjust the Schedule as Needed
Regularly review maintenance records and assess the effectiveness of your preventive maintenance programme. If certain equipment is still experiencing frequent issues, you may need to adjust the schedule or consider additional measures. Ongoing monitoring ensures that your maintenance strategy remains effective over time.
The Long-Term Impact of Preventive Maintenance
Investing in preventive maintenance scheduling yields significant long-term benefits for businesses. By keeping equipment in top shape, companies can avoid expensive repairs, extend the life of their assets, reduce downtime, and improve energy efficiency. These cost savings contribute directly to a healthier bottom line, while enhanced safety and regulatory compliance further protect the business from potential risks.
Conclusion
Preventive maintenance scheduling is a proactive and cost-effective approach to managing equipment and minimising downtime. By implementing a well-planned preventive maintenance programme, supported by modern software tools, businesses can achieve significant cost savings and maintain smooth operations. Whether you’re looking to reduce emergency repair costs, extend equipment life, or improve energy efficiency, preventive maintenance scheduling is a proven strategy for achieving these goals.
For businesses aiming to optimise their maintenance processes, investing in preventive maintenance scheduling software can simplify the planning process and ensure that equipment stays in optimal condition. Take the first step towards a more efficient, cost-effective maintenance strategy today.
This reworded version highlights the benefits and practices of preventive maintenance scheduling while incorporating the role of software solutions to simplify and optimise maintenance efforts.
Get started
Ready to supercharge your Integration business?
An array of tools designed to simplify internal processes, enhance quality control, and boost stakeholder engagement. Generate more accurate customer data and project insights while enhancing internal communication and
efficiencies.
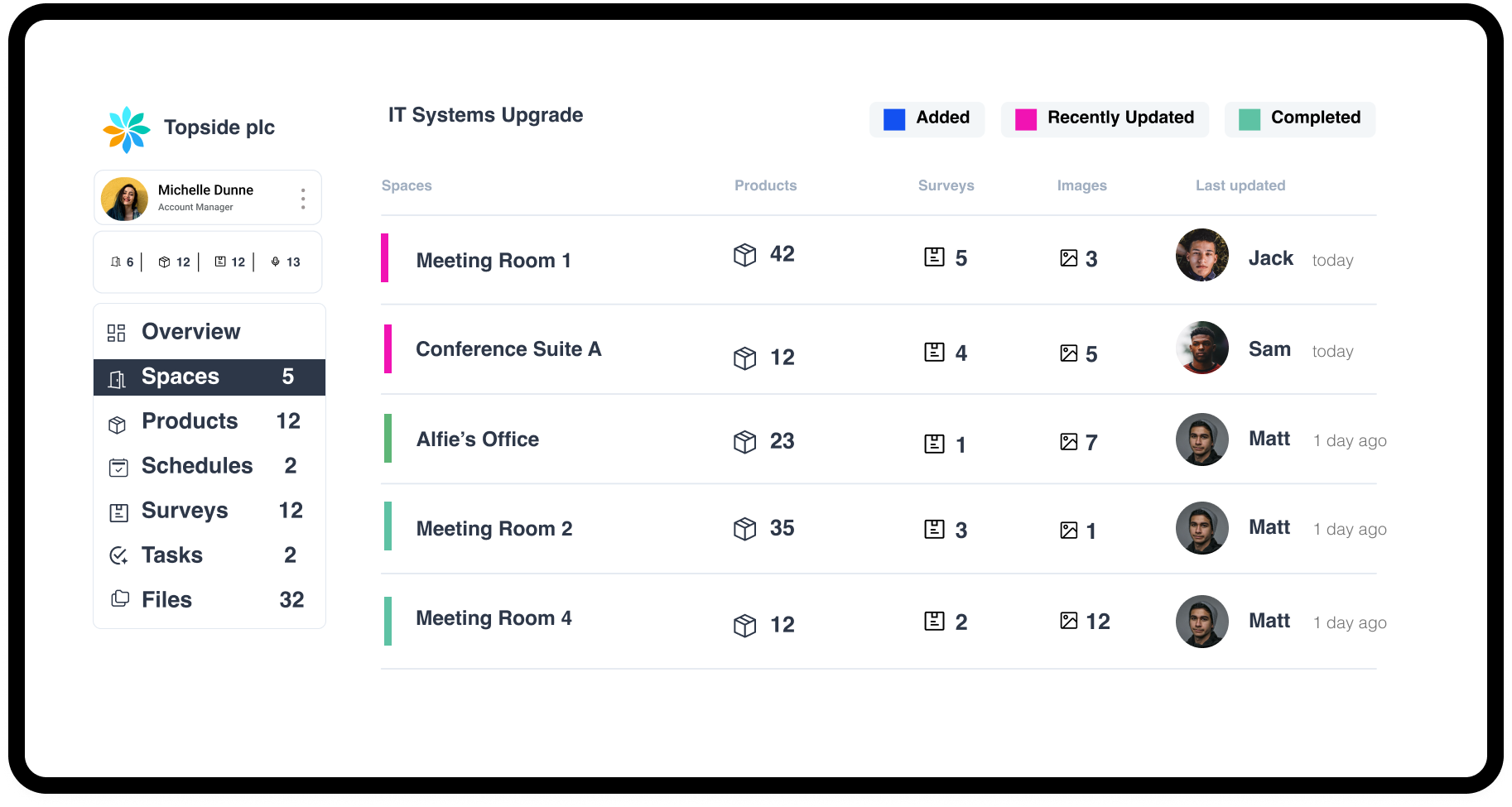
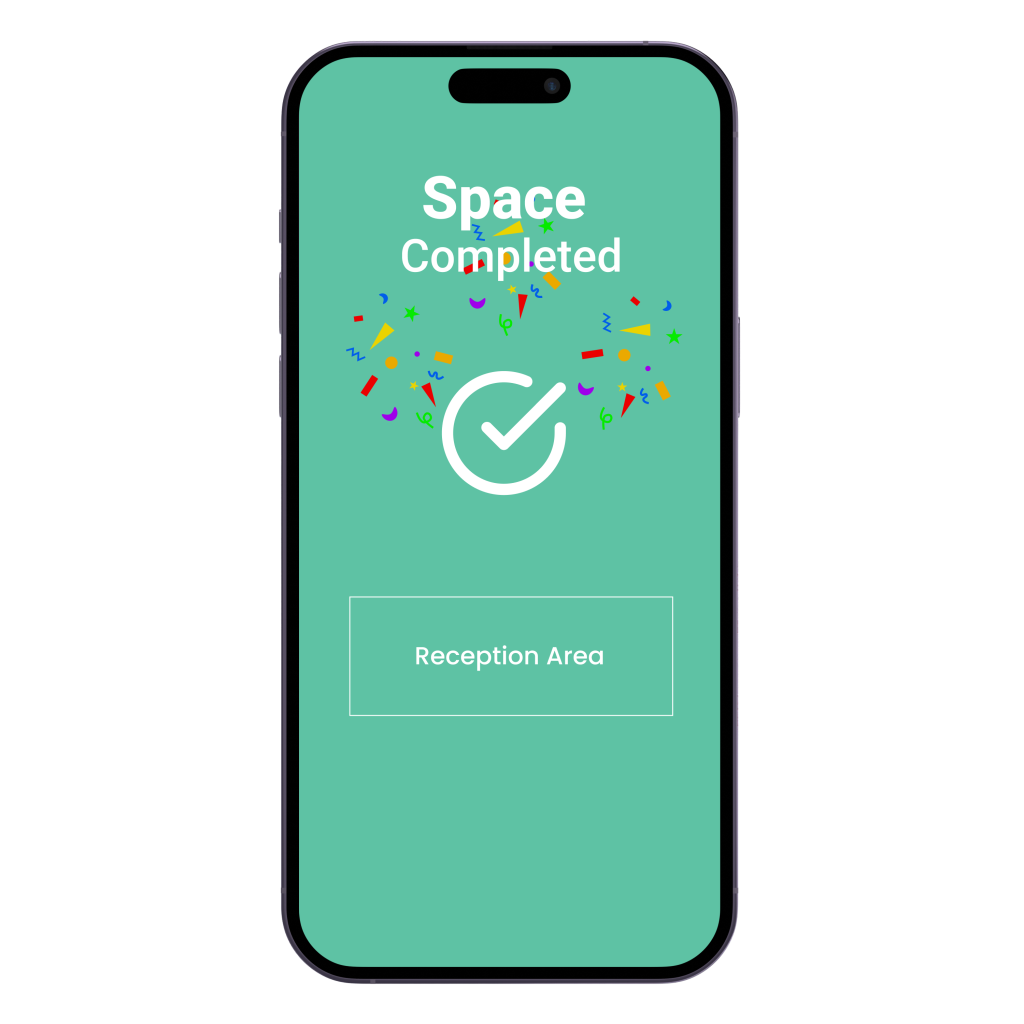